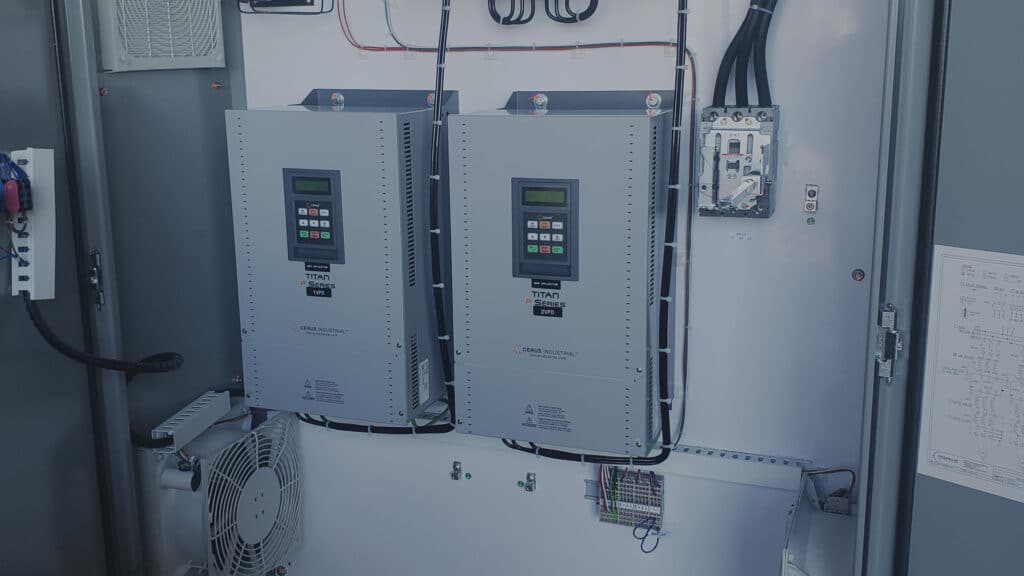
Variable Frequency Drives (VFDs) have become a game-changer in the world of pump systems. They offer a way to control the speed of pumps, leading to significant energy savings and improved system performance. But how exactly does a VFD affect pump efficiency? Let’s delve into this topic.
Understanding Pump Efficiency
Pump efficiency is a measure of how well a pump converts electrical energy into hydraulic energy. It’s calculated by dividing the hydraulic power output by the electrical power input. The higher the efficiency, the less energy is wasted in the pumping process.
The Role of VFDs in Pump Efficiency
A VFD controls the speed of a pump by adjusting the frequency and voltage of the power supplied to the motor. By doing so, it allows the pump to operate at its most efficient point for any given flow rate. This is a significant departure from traditional pump systems that run at a constant speed, regardless of the system demand.
1. Energy Savings with VFDs
One of the main ways that VFDs improve pump efficiency is through energy savings. In many pump systems, the demand varies throughout the day. For example, a water supply system may experience high demand in the morning and evening but low demand at other times.
In a traditional system running at a constant speed, the pump would use the same amount of energy all day, even during periods of low demand. This leads to significant energy waste.
With a VFD, the pump speed can be adjusted to match the demand. During periods of low demand, the pump can slow down, using less energy. This can result in substantial energy savings, improving the overall efficiency of the pump system.
2. Improved Process Control
Another way that VFDs enhance pump efficiency is through improved process control. With a VFD, the pump speed can be precisely controlled to maintain pressure, flow, or other system parameters. This results in better overall system performance and less energy waste.
For example, in a pressure control application, a VFD can adjust the pump speed to maintain a constant pressure, regardless of changes in demand. This eliminates the need for pressure-reducing valves, which can cause significant energy loss.
3. Reduced Wear and Tear
By allowing pumps to operate at lower speeds during periods of low demand, VFDs can also reduce the pump’s wear and tear along with the other system components. This can extend the lifespan of the equipment, further improving the overall efficiency of the pump system.
Challenges and Solutions
While VFDs offer many benefits, they also present some challenges. One of the main issues is heat generation. Because VFDs convert electrical energy into mechanical energy, they generate heat. If not properly managed, this heat can damage the VFD and reduce its lifespan.
To address this issue, VFDs often come with built-in cooling systems. These can be air-cooled or liquid-cooled, depending on the size and requirements of the VFD.
Another challenge is harmonics. Harmonics are distortions in the power supply that can cause problems in other equipment connected to the same power source. To mitigate this issue, VFDs often include filters or other harmonic mitigation techniques.
In conclusion, Variable Frequency Drives play a crucial role in enhancing pump efficiency. They provide significant energy savings, improved process control, and reduced wear and tear on equipment. Despite the challenges they present, with proper management and mitigation techniques, VFDs can greatly enhance the efficiency and effectiveness of pump systems.